Der Fertigungssektor zählt zu den dynamischsten Branchen. Heute wird unermüdlich nach höherer Präzision und Genauigkeit gestrebt. Prozesse wie Drahterodieren, die präzise Ergebnisse liefern, sind für die Branche geradezu transformativ.
Was genau ist Drahterodieren und warum wird es als bahnbrechende Neuerung für die Fertigungsindustrie angesehen? Der folgende Text beleuchtet die Grundlagen dieser anspruchsvollen Fertigungstechnik und ihre Anwendungsmöglichkeiten in verschiedenen Branchen.
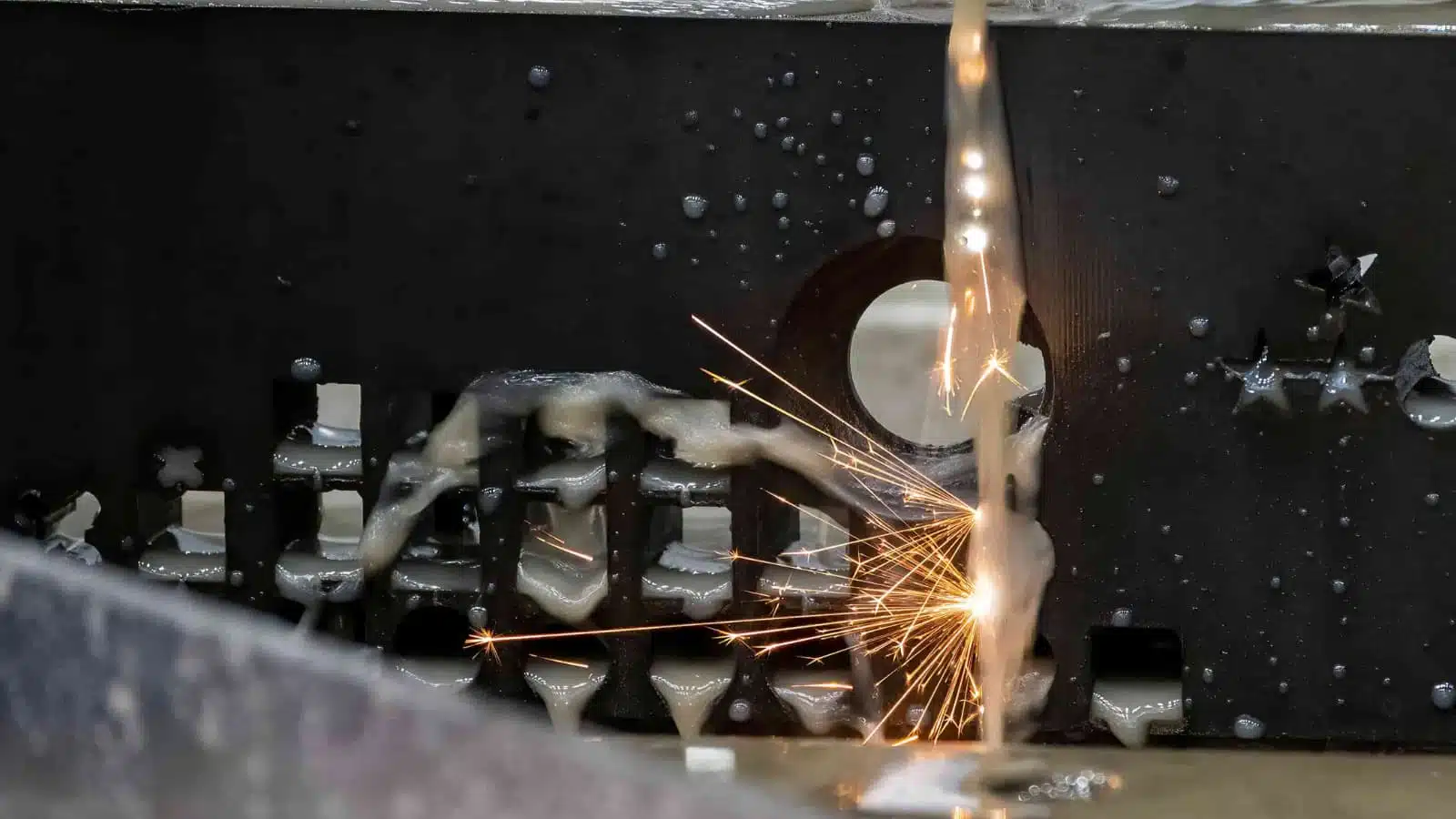
Eine kurze Einführung in das Drahterodieren
Die Drahterosion (EDM) wurde in den 1940er Jahren von zwei sowjetischen Wissenschaftlern entwickelt, die erstmals Metall mittels elektrischer Entladung erodierten. Die Technologie erlebte in den 60er und 80er Jahren bedeutende Fortschritte und setzte sich in der Fertigung zunehmend kommerziell durch. Ende der 90er Jahre wurden Drahterodiermaschinen dank IT- und CNC-Verbesserungen zunehmend computergesteuert, was ihre Effizienz und Präzision steigerte.
Heute ist die Drahterodierung in Branchen wie der Luft- und Raumfahrt, der Automobilindustrie und der Medizintechnik unverzichtbar und bekannt für die Herstellung komplizierter Designs und komplexer Formen, die mit herkömmlichen Bearbeitungsmethoden nicht erreicht werden.
Der Drahterodierprozess
Drahterosion (EDM) ist ein präzises Verfahren, bei dem kontrollierte elektrische Funken zum Schmelzen winziger Teile eines Werkstücks eingesetzt werden. Die Drahtelektrode, typischerweise aus Messing oder verzinktem Material, erzeugt den Funken und bewegt sich entlang einer vorgegebenen Bahn. Der Vorteil? Sie arbeitet berührungslos und verhindert so Schäden oder Spuren am Werkstück und am Werkzeug.
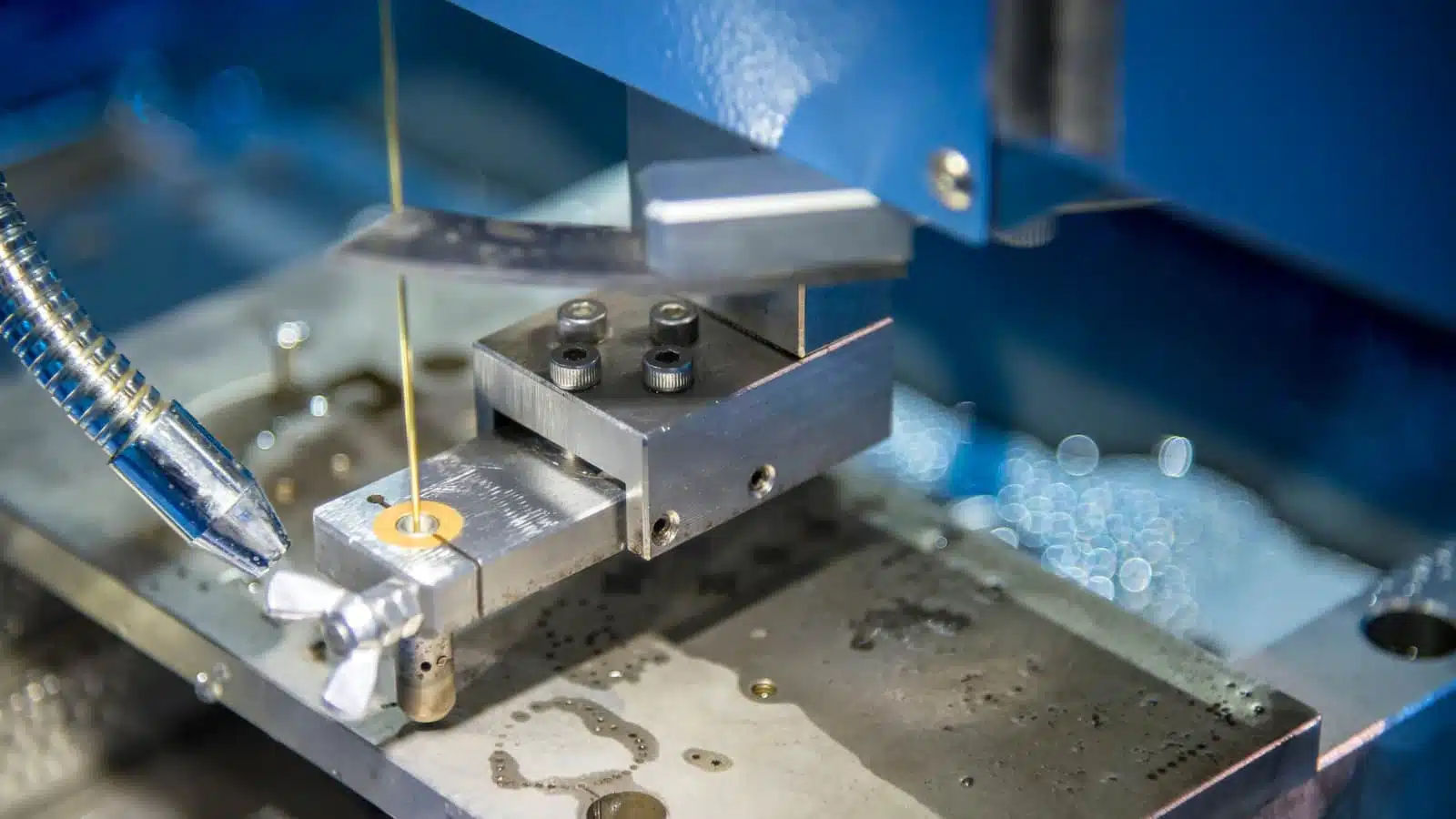
So funktioniert EDM
Das Funkenerosive Laserschneiden (EDM) basiert auf der thermischen Energie elektrischer Entladungen. Diese Entladung erhitzt das Werkstück bis zum Schmelzpunkt und bildet winzige Plasmakanäle. Diese oft mikrometergroßen Kanäle können schnell wieder verschwinden.
Der EDM-Prozess erfolgt in einem dielektrischen Medium, üblicherweise deionisiertem Wasser. Diese Flüssigkeit kühlt das Werkstück und entfernt verdampftes Material, was eine kontinuierliche Bearbeitung ermöglicht.
Bedeutung der Drahtelektrode
Die Drahtelektrode ist sowohl Schneide- als auch Leiterfunktion und somit unerlässlich. Beschichtet mit Materialien wie Messing oder Zink widersteht sie Reaktionen bei hohen Temperaturen. Computergesteuert sorgt sie für präzise Schnitte mit minimaler Verformung und hoher Präzision.
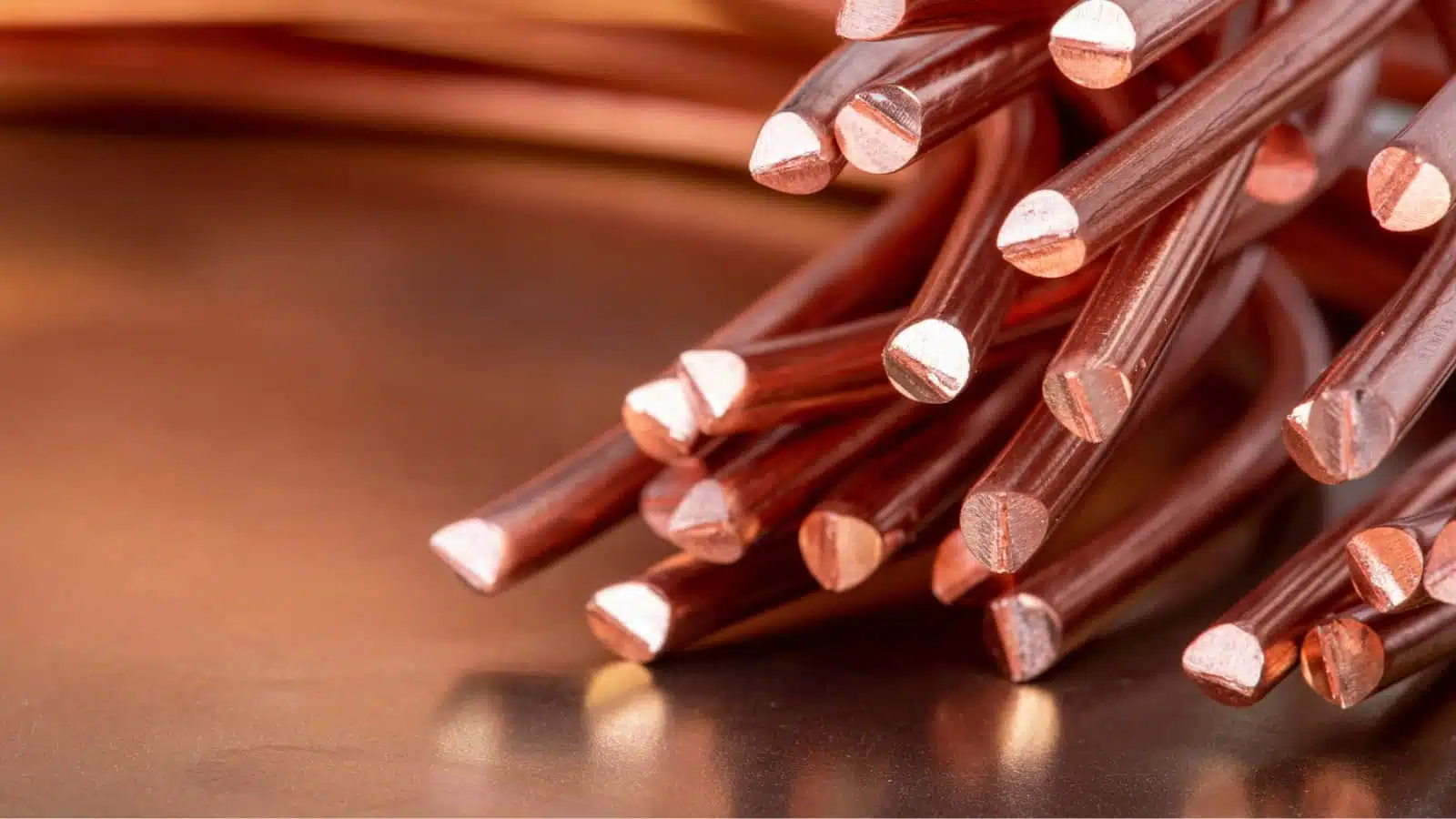
Toleranzen für Drahterodieren
Drahtschneiden gehört zu den präzisesten Fertigungsverfahren überhaupt. Enge Toleranzen sind daher keine Seltenheit. Die tatsächliche Toleranz hängt von verschiedenen Faktoren ab, darunter der Komplexität des Projekts, den Bearbeitungsmöglichkeiten und den Fähigkeiten des Bedieners.
Allerdings sind die Standard- und zulässigen Toleranzen ein Branchenmaßstab, an dem sich viele Hersteller orientieren.
Standardtoleranz und Feintoleranz
Standardtoleranz
Lineare Toleranzen: Sie liegen normalerweise im Bereich von ±0,005 bis ±0,001 Zoll (0,127 bis 0,0254 mm) und geben die zulässige Abweichung für Merkmale wie Löcher, Schlitze oder Profile an.
Toleranzen des Lochdurchmessers: Normalerweise zwischen ±0,0005 und ±0,001 Zoll (0,0127 bis 0,0254 mm), um sicherzustellen, dass die bearbeiteten Löcher innerhalb des definierten Durchmessers bleiben.
Feine Toleranz
Lineare Toleranzen: Erreicht Präzision im Mikrometerbereich, typischerweise im Bereich von ±0,0002 bis ±0,0001 Zoll (0,0051 bis 0,00254 mm), unerlässlich für Anwendungen, die höchste Genauigkeit erfordern.
Lochdurchmessertoleranzen: Bereiche von ±0,0001 bis ±0,00005 Zoll (0,00254 bis 0,00127 mm), was die außergewöhnliche Präzision des Drahterodierens unterstreicht.
Faktoren, die die Toleranzen beim Drahterodieren beeinflussen
Drahterodieren ist für seine Präzision im Mikrometerbereich bekannt und eignet sich daher ideal für komplexe Anwendungen. Die Präzision ist jedoch nicht festgelegt und hängt von mehreren Faktoren ab:
•Maschinenstabilität: Eine stabile Maschine gewährleistet eine bessere Präzision beim Schneiden.
Drahtqualität und -durchmesser: Reinheit, Durchmesser und elektrische Eigenschaften beeinflussen den Bearbeitungsprozess. Optimale Ergebnisse erfordern ein ausgewogenes Verhältnis zwischen Drahtqualität und Durchmesser.
•Werkstückmaterial: Während einige Materialien für Maschinen leichter zugänglich sind, muss die Materialauswahl den Anforderungen der Anwendung entsprechen.
•Spülbedingungen: Der Fluss des dielektrischen Mediums beeinflusst die Qualität des Bearbeitungsprozesses, unterstützt den Materialabtrag, sorgt für gleichmäßige elektrische Entladungen und eine effektive Wärmeableitung.
•Kalibrierung und Wartung der Maschine: Die Leistungsfähigkeit der Maschine ist entscheidend. Hochwertige Maschinen mit erfahrenen Bedienern sind für das Erreichen optimaler Toleranzen unerlässlich.
Thermische Stabilität: Um die bekannte Präzision des Drahterodierens aufrechtzuerhalten, sind kontrollierte Lichtbögen entscheidend. Thermische Instabilitäten können die Genauigkeit gefährden, was die Bedeutung konstanter Bedingungen unterstreicht.
Die am besten geeigneten Materialien zum Drahtschneiden
Eisenmetalle
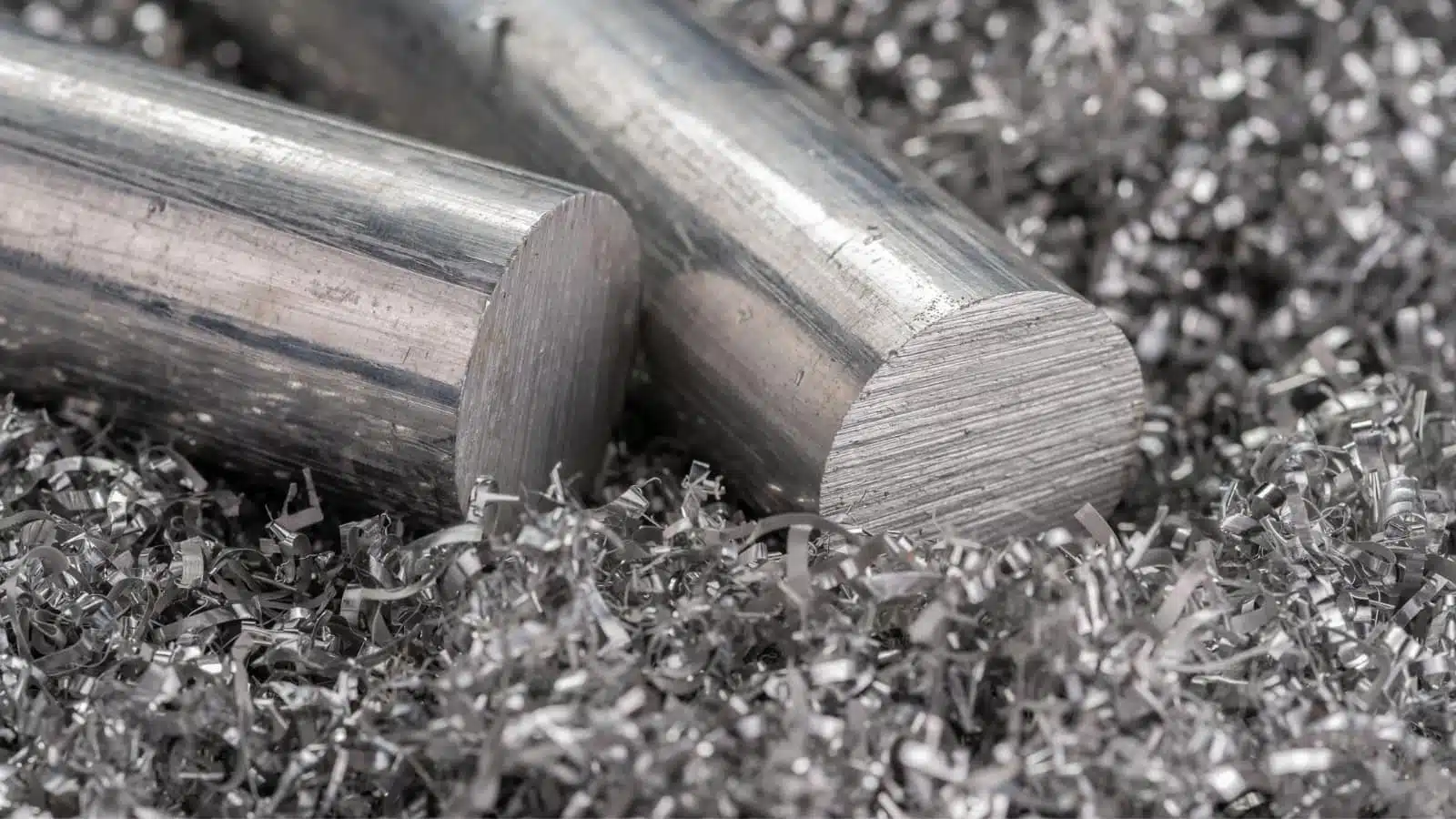
Edelstahl
Es vereint Langlebigkeit mit hervorragender elektrischer Leitfähigkeit. Seine Korrosionsbeständigkeit macht es zu einem gefragten Werkstoff in verschiedenen Branchen. Bei der Bearbeitung zeichnet es sich durch seine Kompatibilität mit präzisen und detaillierten Designs aus.
Werkzeugstahl
Werkzeugstahl ist für seine Härtung bekannt und bildet das Rückgrat vieler Hochleistungswerkzeuge und Präzisionsteile. Seine inhärente Zähigkeit, gepaart mit seinen elektrischen Eigenschaften, macht ihn zu einem idealen Kandidaten für komplexe Details und lang anhaltende Schärfe.
Kohlenstoffstahl
Kohlenstoffstahl ist ein vielseitiger Werkstoff im Metallbereich. Obwohl er weniger gut bearbeitbar ist als vergleichbare Werkstoffe, lässt er sich mit der richtigen Elektrodenwahl und den richtigen Betriebsparametern optimal bearbeiten. Seine Erschwinglichkeit und seine hohe Leistung machen ihn zu einem unverzichtbaren Werkstoff in vielen Branchen.
Legierter Stahl
Legierter Stahl ist eine Kombination verschiedener Elemente und seine Leistungsfähigkeit hängt von seinen Komponenten ab. Je nach individueller Zusammensetzung bietet er Festigkeit, Haltbarkeit und Bearbeitbarkeit und ist somit eine dynamische Wahl für vielfältige Anwendungen.
Nichteisenmetalle
Titan
Titan wird oft als „Weltraummetall“ bezeichnet. Seine Robustheit und sein hoher Schmelzpunkt stellen bei konventioneller Bearbeitung eine Herausforderung dar. Bei der Bearbeitung mit Präzisionswerkzeugen entstehen jedoch komplexe und zugleich robuste Designs, die es zu einem beliebten Werkstoff in der Luft- und Raumfahrt sowie der Medizinbranche machen.
Aluminium
Aluminium, der Liebling unter den Leichtmetallen, wird für seine hervorragende elektrische Leitfähigkeit und Formbarkeit geschätzt. Es lässt sich nicht nur leicht bearbeiten, sondern bietet auch Festigkeit ohne Gewichtsbelastung und ist daher in Branchen wie Transport und Verpackung von zentraler Bedeutung.
Kupfer
Kupfer ist ein hervorragender Leiter und das Herzstück vieler elektrischer und elektronischer Wunderwerke. Sein natürlicher rötlich-orangefarbener Farbton und die Möglichkeit, es zu detailreichen Bauteilen zu formen, machen es in allen Bereichen unverzichtbar, von der Elektronik bis hin zur dekorativen Kunst.
Messing und Bronze
Bei diesen Legierungen mit ihren strahlenden Goldtönen geht es nicht nur um Ästhetik. Ihre hervorragenden elektrischen Eigenschaften machen sie zu idealen Werkstoffen für Komponenten, bei denen Präzision auf Schönheit trifft, wie etwa bei kunstvollem Schmuck oder hochwertigen elektronischen Bauteilen.
Wichtige Anwendungen des Drahterodierens in der modernen Technik
Die Drahterodierung gewinnt aufgrund ihrer Vielseitigkeit bei der Bearbeitung unterschiedlicher Materialien und der Möglichkeit, präzise Details und enge Toleranzen zu erzielen, zunehmend an Bedeutung und ist daher in der modernen Fertigung von zentraler Bedeutung. Hier sind drei Hauptanwendungen:
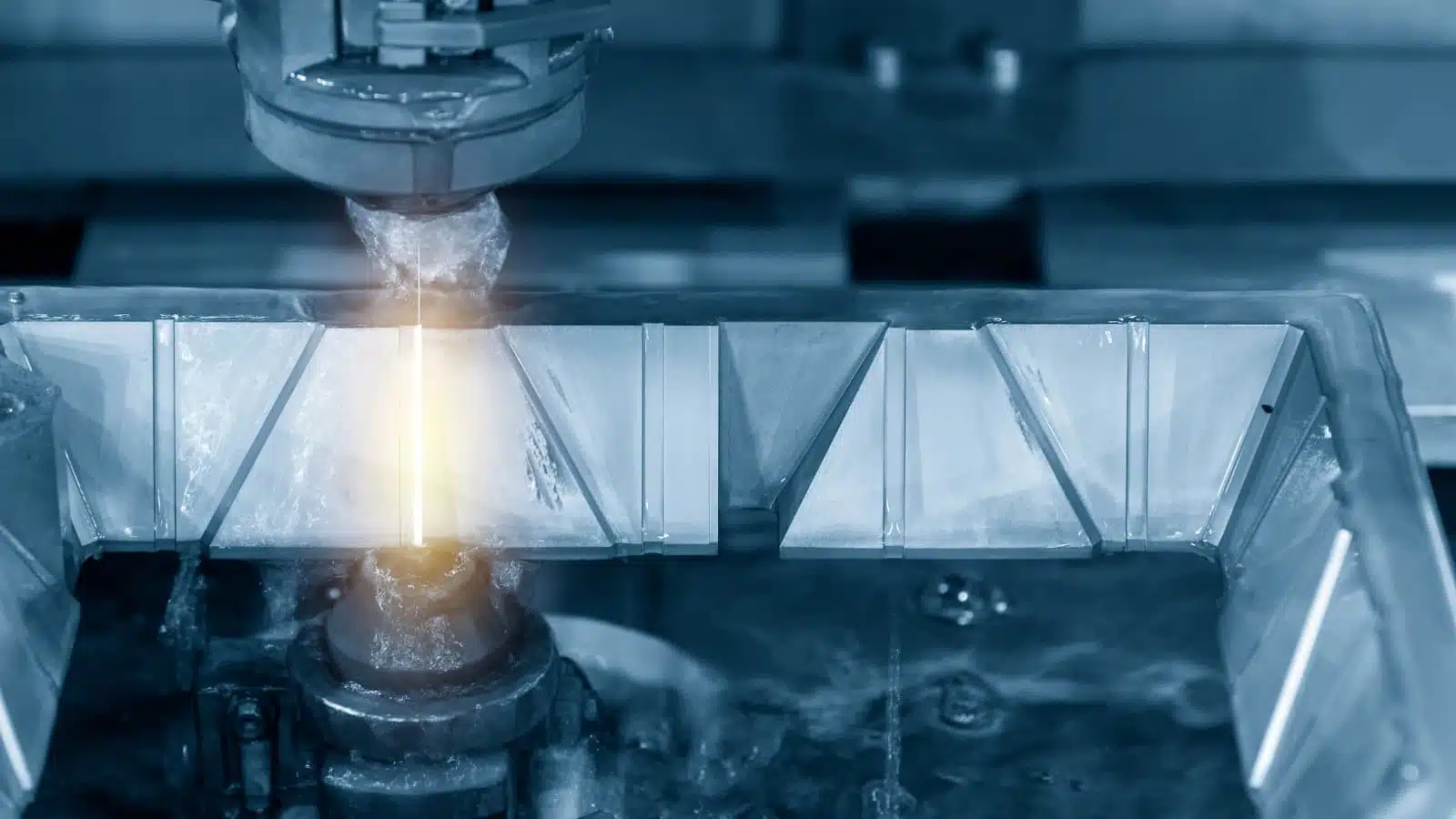
Fertigung von Präzisionsteilen
Die gängige Wahl für die Herstellung hochpräziser Teile mit engen Toleranzen. Es eignet sich hervorragend für die Herstellung komplexer Formen, feiner Details und kleiner Merkmale aus verschiedenen Materialien.
Branchen wie die Luft- und Raumfahrt, die Medizintechnik, die Automobilindustrie und die Elektronikindustrie verlassen sich bei der Herstellung wichtiger Komponenten wie Zahnrädern, Düsen, Verbindungsstücken und komplizierten Formen auf Drahterodieren.
Werkzeug- und Formenbau
Drahterodieren ist ein wichtiges Verfahren zur Herstellung von Schmiedeformen, Gesenken und Spezialwerkzeugen und deckt Prozesse vom Spritzguss bis zum Stanzen ab. Die präzise Einhaltung exakter Abmessungen und die präzise Fertigung scharfer Kanten gewährleisten höchste Qualität und Einheitlichkeit in der Großserienproduktion.
Prototypenentwicklung
Für schnelles und präzises Prototyping nutzen Ingenieure und Innovatoren das Drahterodieren. Dies beschleunigt die Designvalidierung und strenge Testphasen.
Durch Drahterodieren hergestellte Prototypen spiegeln das Endprodukt sehr genau wider und unterstreichen so seine Bedeutung im Produktentwicklungszyklus.
Aufgrund seiner Stärken in diesen Kernbereichen werden die präzisen und genauen Fähigkeiten des Drahterodierens in zahlreichen Branchen umfassend genutzt.
•Herstellung medizinischer Geräte
• Elektronik und Mikrokomponenten
•Luft- und Raumfahrt
• Schmuck und Uhrmacherei
•Automobilindustrie
•Energiesektor
•Formen- und Matrizenreparatur
Veröffentlichungszeit: 12. Dezember 2023